Conveyors
From lightweight lighting fixtures to 6,000‑lb tractor frames, GAT engineers and fabricates conveyor systems that keep your production line flowing—precisely paced to washer, oven and spray‑booth cycle times.
Why Choose a GAT Conveyor?
Advantage | Engineering Detail | Production Payoff |
---|---|---|
Right‑Sized Capacity | 200‑lb enclosed track up to 6,000‑lb I‑Beam 6" | No over‑ or under‑spec cost |
Modular Architecture | Bolt‑together drives, curves, verticals | Rapid install & reconfiguration |
Smart PLC Control | VFD speed, recipe indexing, load tracking | Sync takt time & reduce WIP |
Low‑Maintenance Design | Sealed bearings, oil‑bath gearboxes, auto‑lube chain options | Higher uptime, lower labor |
Safety & Compliance | CAT‑3 e‑stops, anti‑runaway brakes, guarding packages | Meets OSHA & DIN 858 standards |
Conveyor Types
This type of conveyor is comprised of a series of trolleys that transport products and materials by an overhead track connected to a looping chain. They can run in multiple directions, and function horizontally and vertically. Because the track is enclosed, contamination can be prevented from reaching the chain and open surfaces, thus reducing the need for cleaning and maintenance costs. This type of conveyor can typically process items weighing up to 300 lbs.
One of the most common types of conveyors, I-Beam systems, come in 3″, 4″, or 6″ designs where the chain rides on a I-Beam. This type of conveyor is used for products with weight capacities from 75 lbs up to 5,000 lbs.
When your application calls for loading heavy or large parts, a power & free conveyor system will allow for greater line layout flexibility.
These conveyors move product down the line on a flat surface made up of mesh wires that form a perforated layer. Mesh belts offer many applications and can accommodate various styles of belting options. They typically do not contain curves or inclines/declines.
A chain conveyor moves material through production lines by using a powered continuous chain with a series of single pendants. It is driven by a single motor that powers the movement of the pendants and the suspended items they hold. Crossbars mount to the top of the conveyor drive and provide a platform for mounting trays.
Wickets are formed wire frames that support moving products in a near-vertical position. This arrangement permits product accommodation from one stage of production to the next. It also allows for temperature control and evenness of cure because of the air circulating between wickets and/or the parts.
A drum-style system is used to process smaller, uniform type parts through a “auger” style of rolled drum which provides for pre-treatment wash and dry-off applications.
PLC & Controls
Auto start and shutdown
Calendar and time basis with operator acknowledgement required.
Auto pump on/off with conveyor operation
Sync conveyor movement with pump operation as well as sequential pump start to lower power in rush.
Sequenced startup and shutdown capability
Pre-program your equipment to auto-start and shut down after certain tasks have been completed.
Productivity Analysis
Productivity analysis charts show the percentage of time your conveyor has been running each day, and who was controlling the starts and stops.
Fault Log
Active fault logging and password protection to improve security and improve preventative maintenance.
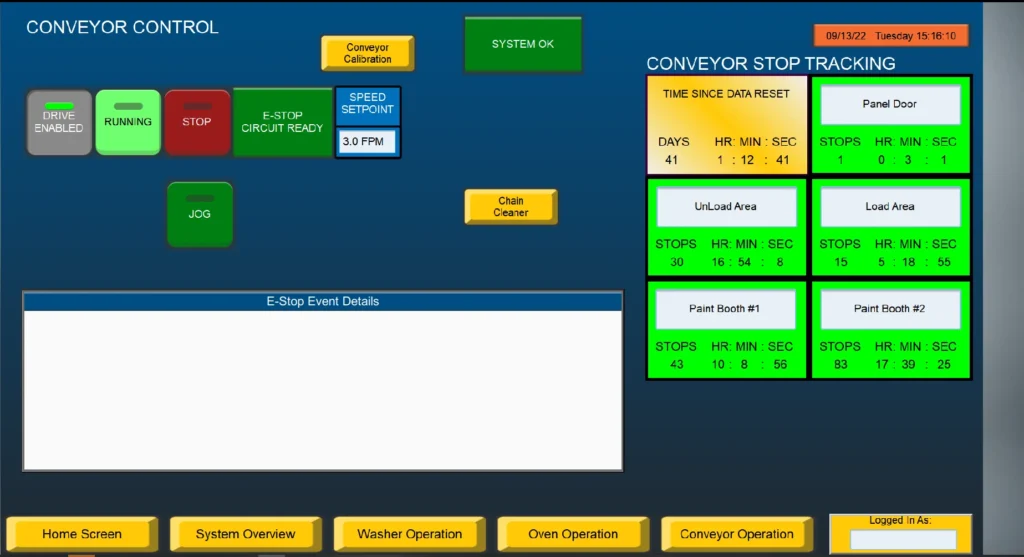
Performance Metrics
- ±1 fpm speed repeatability with VFD drives.
- >98 % mechanical uptime on PM‑plan customers.
- 30 % floor‑space reduction vs. floor conveyors when switching to overhead ET‑400.
Seamless Integration With GAT Finishing Lines
GAT conveyors are designed alongside polypropylene washers, process ovens, powder coating rooms and IR booths—ensuring balanced cycle times and single‑source accountability from CAD to commissioning.
Frequently Asked Questions
Can I upgrade a legacy conveyor with power‑and‑free sections?
Yes—our modular P&F drives splice into existing ET or I‑Beam track with minimal downtime.
Do you supply hangers and tooling?
Absolutely—custom racks, hooks and load bars engineered for your parts.
How often does the chain need lubrication?
With auto‑lube, chain service intervals stretch to 2,000 hours; manual systems need weekly checks.