Convection Process Ovens—Workhorse Curing for High‑Speed Finishing Lines
Need reliable, uniform heat day in and day out? GAT’s gas‑fired convection process ovens deliver consistent cure temperatures and tight part‑to‑part repeatability—whether you’re running powder coating, e‑coat, or liquid paint at up to 90 feet per minute.
Why Choose a GAT Convection Oven?
Advantage | Engineering Detail | Production Benefit |
---|---|---|
Direct‑Impingement Airflow | High‑velocity plenums above & below the conveyor | Shorter oven length—higher line speed |
Patented Air‑Seal Vestibules | Dual counter‑flow curtains | Prevents heat loss, lowers gas by up to 15 % |
6‑Inch Mineral‑Wool Panels | Tongue‑and‑groove, 18‑ga skins | ±5 °F uniformity across the belt |
NFPA 86 Class A Gas Train | Maxon burners, proof‑of‑closure, leak‑test valves | Code compliance out of the crate |
Modular 24‑Inch Sections | Bolt‑together frames, tool‑free access doors | Scales with takt time and new models |
Tool‑Free Clean‑Out | Hinged nozzles & removable drop pans | 5‑minute maintenance = maximum uptime |
Convection Oven Series & Typical Uses
Series | Max Temp | Standard Module Length | Belt Widths | Ideal Applications |
---|---|---|---|---|
COV‑300 | 450 °F | 6 ft | 36–60 in | Dry‑off after washer, flash‑off wet primer |
COV‑400 | 500 °F | 8 ft | 36–72 in | Full powder cure on mixed‑metal parts |
COV‑HD | 600 °F | 8 ft | 48–84 in | Heavy steel, castings, thick coatings |
The GAT Difference
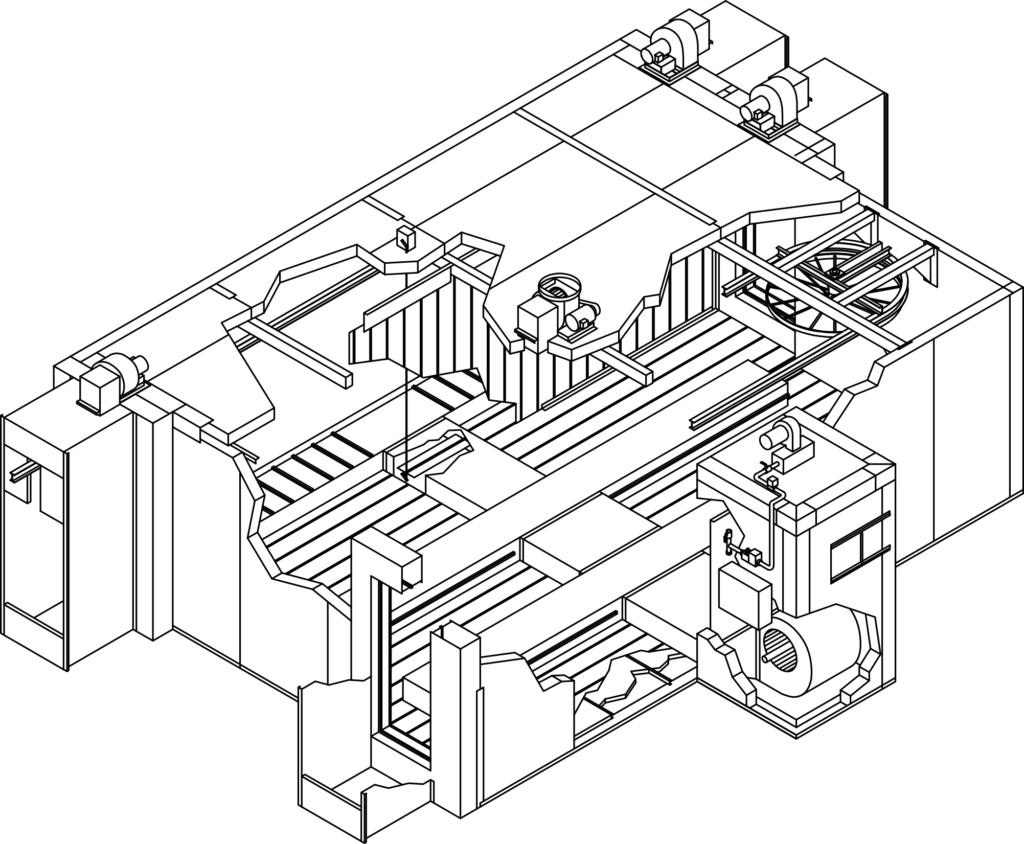
18-gauge galvannealed steel with a 12-gauge internal frame makes up the floor-mounted ductwork
6″ thick steel encased 4# density batt mineral wool insulated panels provided in four-foot widths
Allows ovens to operate more efficiently due to lowered exhaust rates and reduction of heat loss.
Present 45% fewer seams, thereby reducing through steel and increasing efficiency.
Factory Built and tested heater assembly. Custom designed for BTU and CFM output required for any job.
Spot welded and clip assembled design allows for 20x less through steel than our competitors resulting in a decreased thermal footprint and reduced gas bills.
Allows quick purge and optimal oven exhaust rating for efficient and continuous operation. Ultimately allows for more production hours per day.
Features & Benefits
- Direct air impingement along with heated air.
- 18-gauge galvannealed steel with a 12-gauge internal frame makes up the floor-mounted ductwork.
- Top mounted, adjustable louvers allow for direct air impingement on the part.
- Directed air streams = reduced drying temperatures.
- Six-inch-thick steel encased 4# density batt mineral wool insulated panels provided in four-foot widths.
- High-velocity air-seals.
- Edges of dry-off oven panels are arranged to fit in tongue-and-groove.
- Dry-off oven panels uses an isolated spreader clip and stiffener channel construction.
- Gas-fired modulating burner controlled via a UL, FM, and NFPA compliant gas train.
- Dry-Off oven panels are sheathed inside and out with 18-gauge galvannealed steel – reinforced with stiffening ribs spaced on 12-inch centers.
- Conveyor openings through the side of the dry off oven.
- High air turnover along with floor mounted ductwork.
- Seams are fully insulated with the same insulation material as the oven panels. Construction of oven panel is entirely spot welded.
- Centrally located thermocouple.
- VFD on exhaust fans allows quick purge and optimal oven exhaust rating for efficient and continuous operation.
- 1/20th of the linear feet of through steel.
- Dries the part more effectively.
- Sturdy build capable of taking on any workload for decades of service.
- Movement at the part is maximized and moisture is removed quickly. Minimizes the potential for flash rusting.
- Operating energy costs are decreased significantly.
- Four-foot-wide panels present 45% fewer seams, thereby increasing efficiency.
- Minimize the heated air in the oven escaping to the surrounding atmosphere, and to insure the optimum efficient operation of the oven.
- Provides a tight seal that also allows for thermal expansion.
- Greatly reduce the amount of through steel to increase efficiency as well as to provide added strength.
- Safer, more efficient burner usage.
- Stronger frame for longer-lasting production.
- High-velocity air seals are provided to minimize the heated air in the oven escaping to the surrounding atmosphere.
- Ensures even temperature throughout the cure oven.
- Smooth surface inside and out.
- Designed for best temp distribution and takes the guesswork out of oven temperature and efficacy.
- Meets and exceeds NFPA requirement and gives more hours out of the day for production.
- Provides lowest heat signature in the industry, reduces gas bill, and saves money over time.
Convection Oven Types
All Convection Ovens designed and developed by GAT are classified as Dry-Off/Cure ovens with various adjustments to meet a specific manufacturing need. Whether you have a liquid or powder finish, our Dry-Off/Cure Ovens are custom designed to fit your space, match your speed, and accommodate any size of manufactured parts.
Do you need an optimized design for your convection oven? Our elevated convection ovens come with side mount or underslung heater locations with conveyor openings through the bottom of the cure to remove any need for seals. The increased efficiency makes our elevated convection ovens a popular choice.
OEM companies ask us for the biggest space saver: outdoor convection ovens. This places the BTU and heat signature outside the plant in a weatherproof design capable of keeping the wind and snow at bay. Our GAT engineering team can factor in additional concrete and trench work to fit your manufacturing needs. There are some challenges when it comes to outdoor convection ovens, namely securing the right permits and initial purchase cost. The extra space you save is worth it over time with how easy and convenient outdoor convection ovens can be for production.
PLC, Smart Controls & Energy Management
Auto start and shutdown
Calendar and time basis with operator acknowledgement required.
Auto pump on/off with conveyor operation
Sync conveyor movement with pump operation as well as sequential pump start to lower power in rush.
Sequenced startup and shutdown capability
Pre-program your equipment to auto-start and shut down after certain tasks have been completed.
Remote monitoring & troubleshooting
Productivity Analysis
Productivity analysis charts show the percentage of time your conveyor has been running each day, and who was controlling the starts and stops.
Fault Log
Active fault logging and password protection to improve security and improve preventative maintenance.
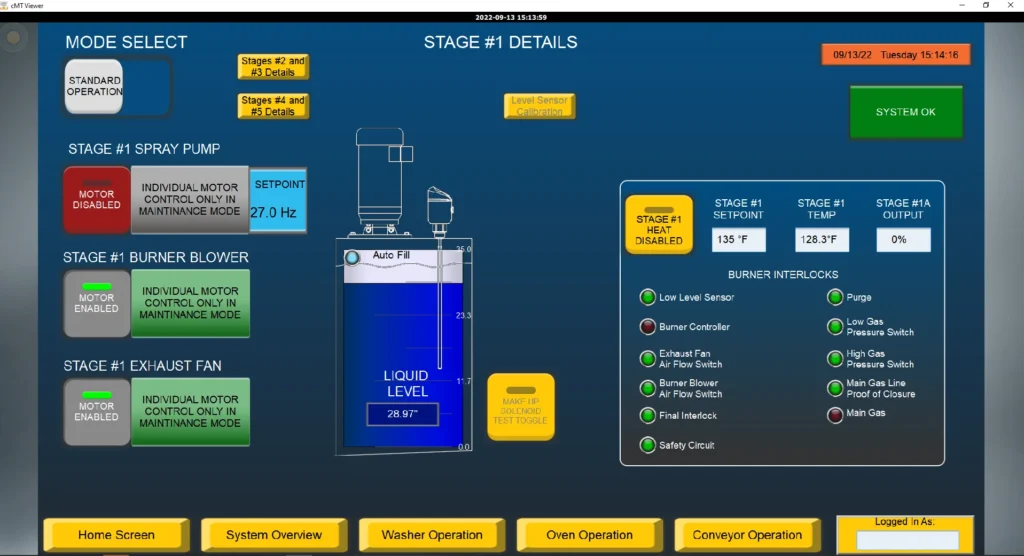
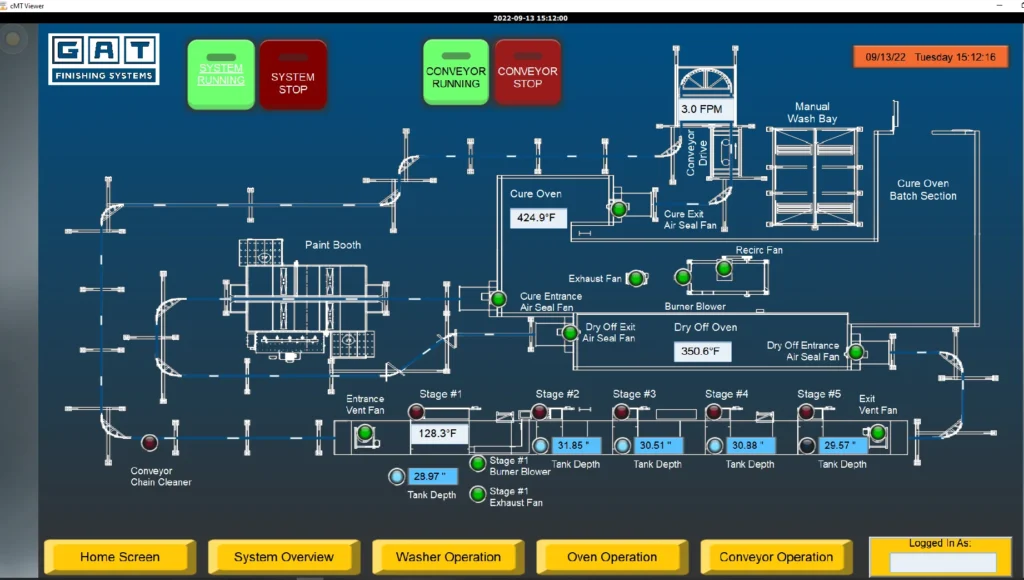
Proven Performance Metrics
- ±5 °F temperature uniformity documented on 9‑point SAT per AMS2750.
- 12‑min cure @ 400 °F for 11‑ga A36 plate, 60‑fpm line speed.
- 15 % average gas savings vs. legacy recirc ovens (air‑seal vestibules).
Seamless Integration
Convection ovens bolt right into GAT polypropylene washers, powder coating rooms, enclosed‑track conveyors and IR booster zones—all designed, built and installed by one accountable partner.
Frequently Asked Questions
Can the same oven cure multiple coating chemistries?
Yes—store separate time/temperature recipes for polyester, epoxy, urethane, or liquid enamel.
Is electric convection available?
Absolutely—SCR‑controlled electric heaters where natural gas is unavailable or ESG targets dictate.
What maintenance is required?
Quarterly filter changes and annual burner tune‑ups keep uptime above 98 %.