Innovations That Power the Modern Finishing Line
Since 1958, GAT has turned real‑world production headaches into patented, field‑proven breakthroughs. Explore the core finishing system innovations that lower energy use, extend equipment life and boost throughput across hundreds of powder‑coat and paint lines.
Ask GAT to Create Your Next Custom Finishing System
Polypropylene
Light. Durable
Many years ago, non-stainless steel was the standard for equipment, but it had many drawbacks. Harsh chemicals and oxidation degrade the steel, requiring it to be regularly replaced. While stainless steel was available and utilized, it comes at a high cost up front and is less efficient to operate.
GAT’s Polypro washer housing, patented in 1991, is the same material used to make the very containers which chemicals are shipped in because it doesn’t break down over time and is more cost effective. Poly housings are non-hygroscopic, so they are ideal for moist environments because they resist scaling. Polypropylene creates energy savings because it requires 20-40% less energy to operate due to its low coefficient of heat transfer, making GAT an early adopter of green finishing practices.
Additionally, Polypropylene allows for improved illumination inside the work atmosphere because it is translucent, thereby making for a safer and higher visibility work environment. GAT’s Poly housings provide unique solutions which benefit the owners and operators as well as the maintenance technician within the plant
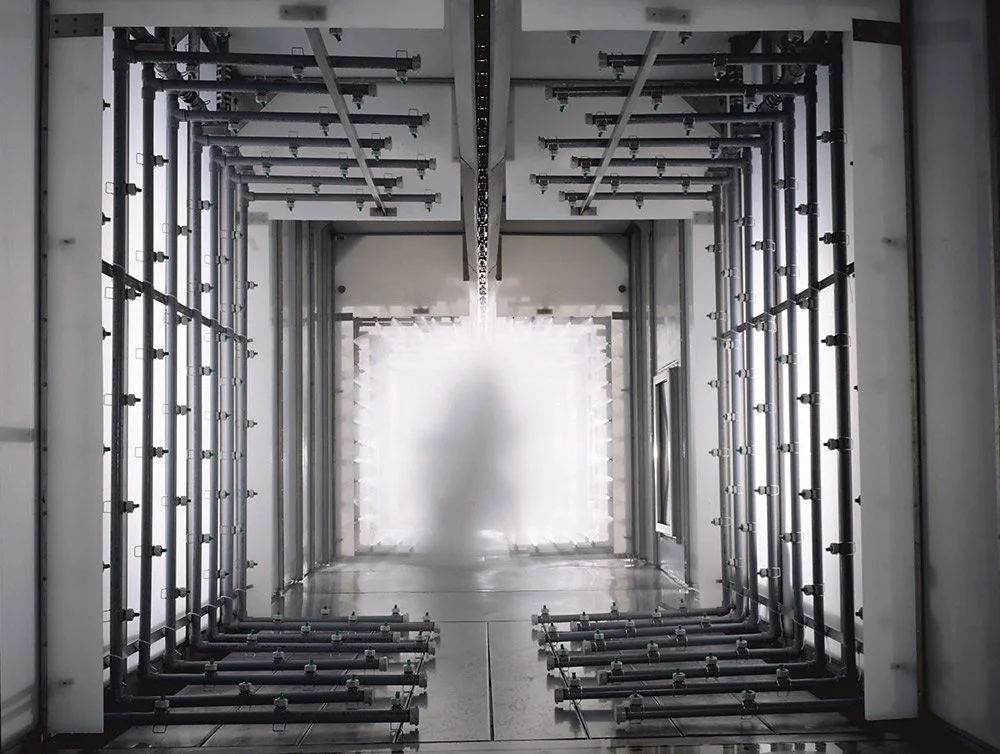
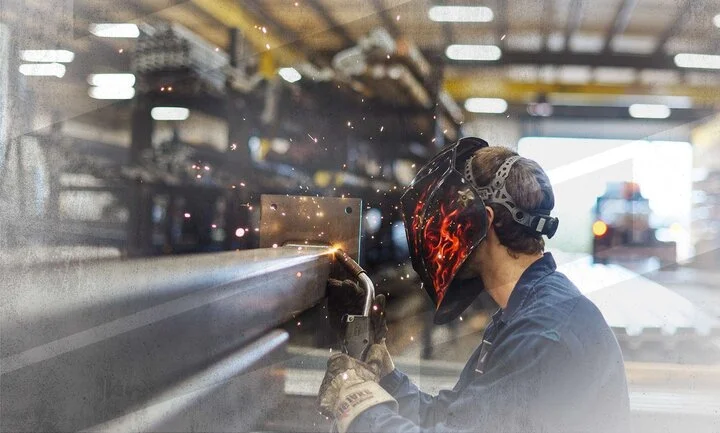
Heat Exchange
Green and EFFICIENT
In the early 1960s, GAT became the original manufacturer of heat exchange optimized equipment. We provide innovative, best-in-class design of high-exchange equipment. Compared to the industry standard GAT equipment doubles the exchange surface area, thus doubling the heat transfer to the tank solution as proven by our industry-leading low exit gas temperature leaving the heat exchanger. This results in lower exhaust rates, less natural gas usage and lower operational costs. By putting more of the heat into the water and less into the stack exhaust, providing profits to the bottom line.
Air Seals
Energy Savings
In 1963, our unique air seals were patented due to their ability to eliminate the need for gravity air seals and allow ovens to operate more efficiently due to lowered exhaust rates and reduction of heat loss. This translates to lower heater box firing rates and greater savings for the client.
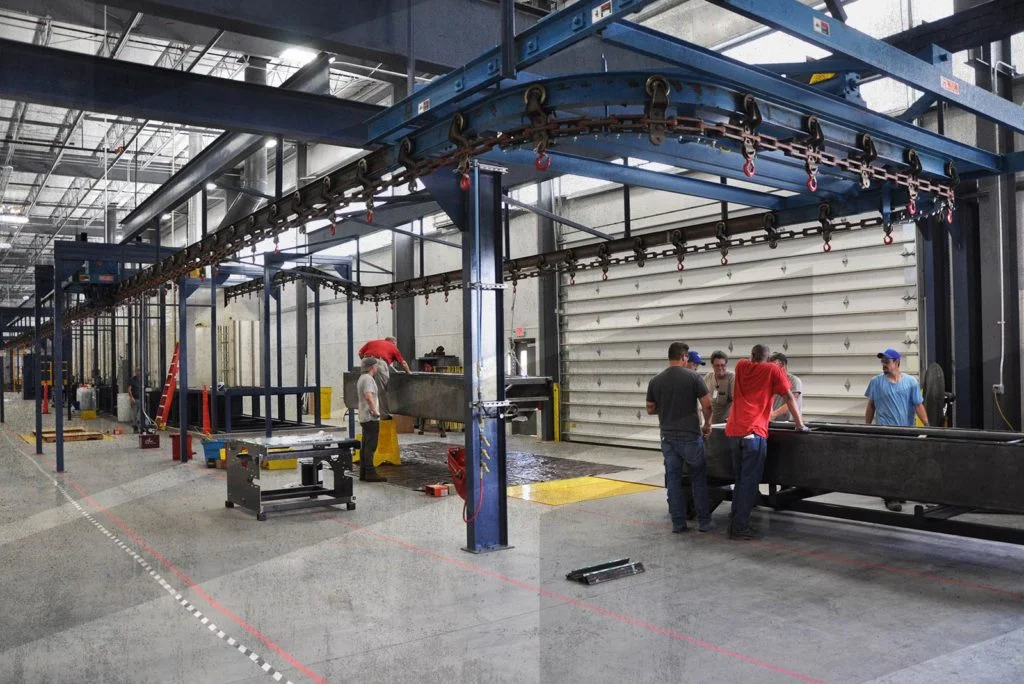
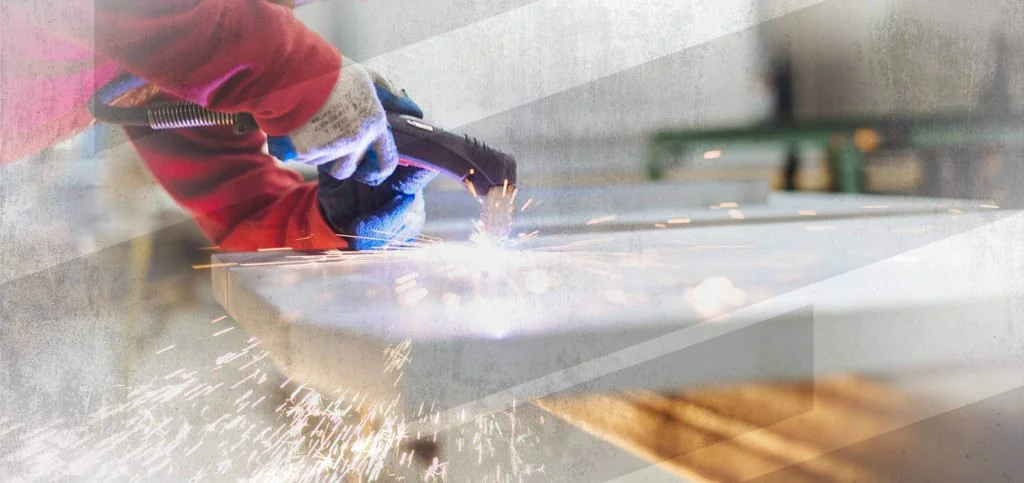
Oven Panel Design
Keep Heat In
Our unique oven panel design uses larger, four-feet wide panels, compared to standard 27” wide panels, that are spot-welded and clip assembled. This allows for a reduction in through steel and uses 1/20th of the seam heat signature compared to standing seam panels. The panels are six inches thick with 4-pound density mineral wool, as compared to the four-inch panels commonly seen in the industry. All of this allows for your ovens to run more efficient by allowing less heat to escape.
Infrared
Small Footprint
GAT’s infrared technology are zone-controlled PLC for hybrid or gel applications. Shipped and assembled and with GAT’s expertise, they can be used to create the capacity for line speed increases or part thickness gains. Factory tested and pre-fired, this gas-catalytic technology has custom and standard design applications.
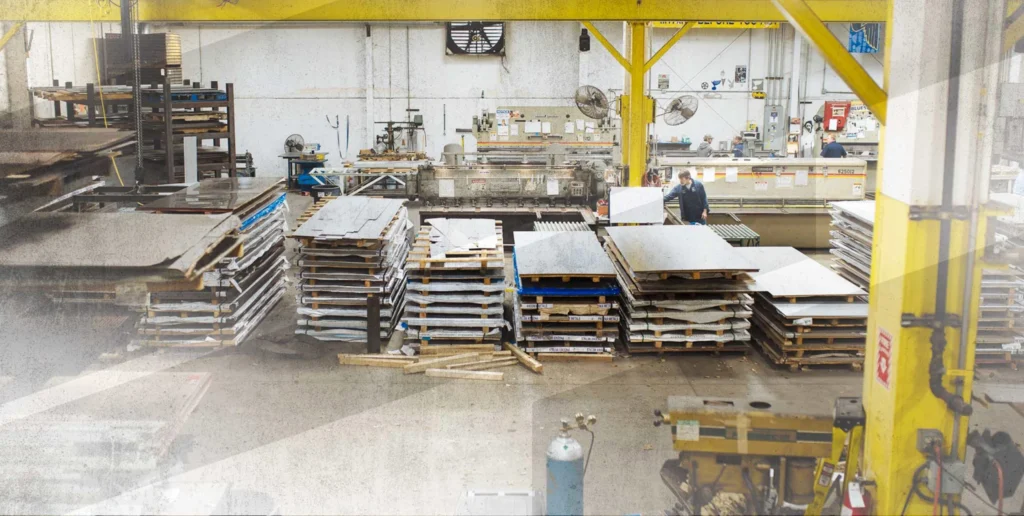
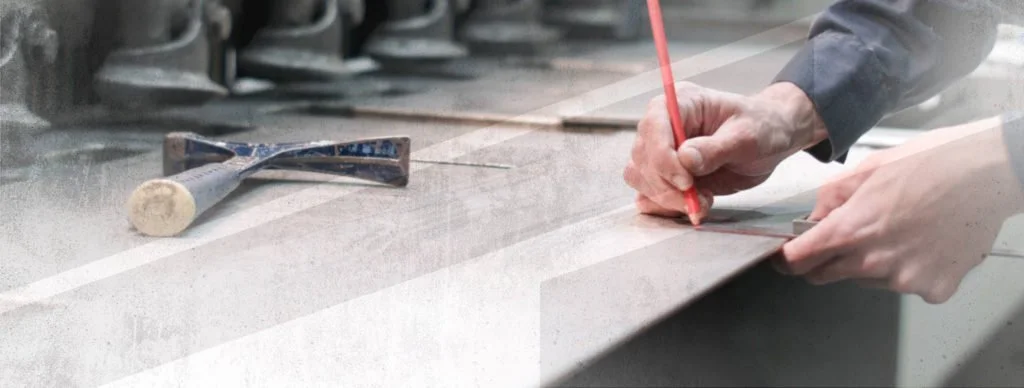
Evaporator
Engineered for Efficiency
A critical part of any finishing system, our innovative evaporators have been engineered with a carbon footprint of zero. They use waste heat from other GAT thermal processes, making them a green alternative for your operations. Our evaporators reduce waste water and operate on heat that has already been created instead of requiring energy.