Installation & Operator Training—Your Finishing Line, Live and Productive
When fabrication is complete, GAT dispatches experienced installation crews and controls engineers to erect, wire, plumb and commission your industrial finishing system—then train your team for safe, efficient production.
Who Can You Trust to Install Your Next Custom Finishing System? There’s only one answer: GAT.
You’re paying for an exceptional finishing system to help your parts look their best. You can’t afford to have just anybody install your system. When it comes to your system installation, the last words you want to hear are “broken,” “missing,” “maybe,” or “wrong.” General Automatic Transfer has a veteran team of trained and experienced installers who take pride in putting our names next to our work. This includes our installation process.
We want to ensure your new custom finishing system is positioned exactly right to function the right way. Nobody knows your system better than we do when it comes to installation. It’s also why we make the installation process as pain-free as possible with turnkey service through startup commissioning.
What Our Turnkey Installation Includes
Phase | Key Activities | Typical Duration |
---|---|---|
Rigging & Placement | Offload, set and anchor washers, ovens, conveyors, booths | 3–5 days |
Utility Hook-Up | Gas trains, electrical drops, compressed air, drains | 2–4 days |
Controls & PLC Integration | Wire panels, I/O checks, load recipes, network HMIs | 2–3 days |
System Alignment & Leveling | Laser align conveyor drives, verify oven seals, calibrate sensors | 1–2 days |
Safety Verification | Test e-stops, light curtains, fire suppression, NFPA clearances | 1 day |
Commissioning & Ramp-Up | Heat-soak ovens, balance airflow, run first-article parts | 2–3 days |
Operator & Maintenance Training | Hands-on instruction, preventive maintenance, troubleshooting | 1–2 days |
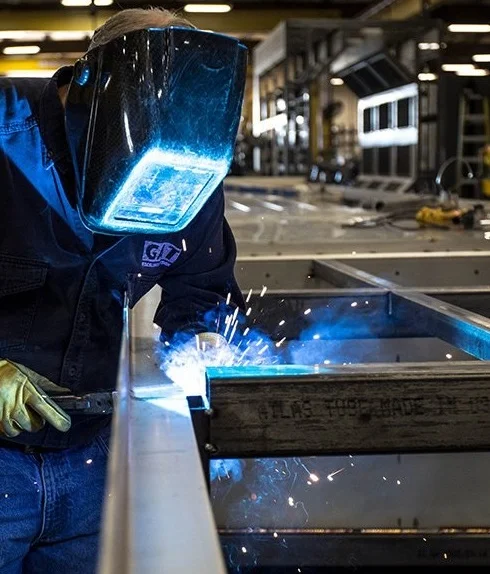
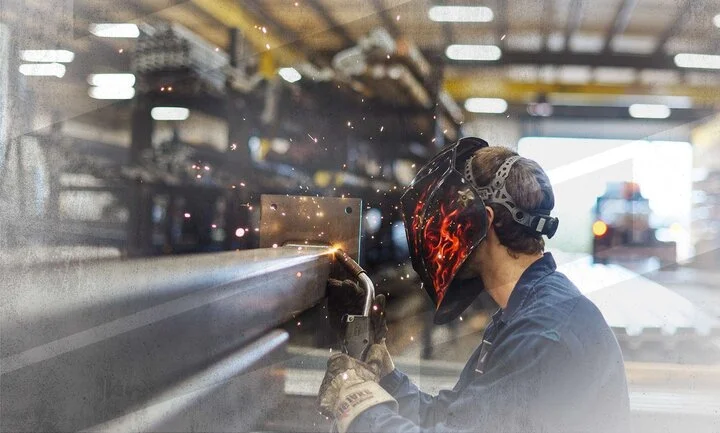
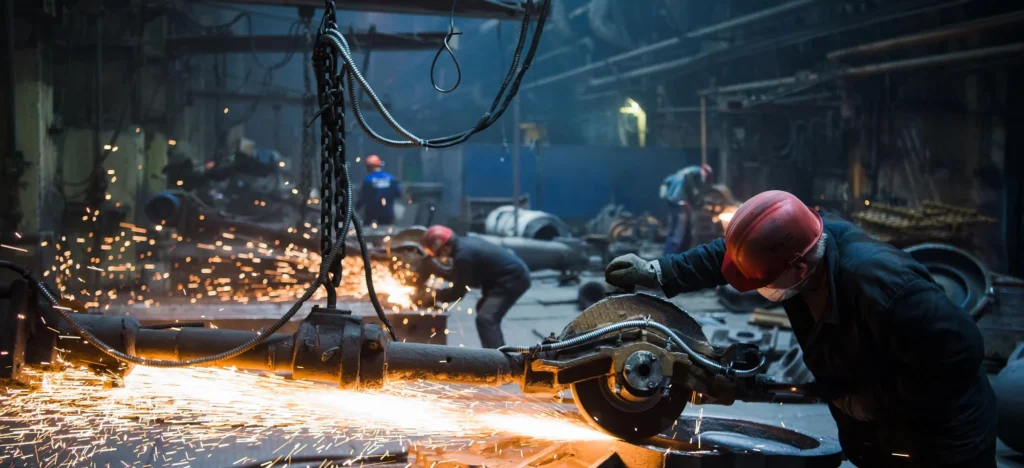
Why GAT Installation Drives Faster ROI
- Factory‑Built Sub‑Modules – Pre‑wired skids and bolt‑together panels cut field hours by up to 30 %.
- Experienced Crews – Average installer tenure is 12 years and 100+ lines commissioned.
- Controls Experts On‑Site – Same engineers who wrote your PLC code fine‑tune it on the floor.
- First‑Pass Quality – 95 % of systems hit spec on the first production run.
Training Deliverables You’ll Receive
- Operator Manuals & Quick‑Start Guides – Step‑by‑step procedures for daily start‑up and shutdown.
- Maintenance Checklists – Weekly, monthly and annual tasks for maximum uptime.
- PLC‑HMI Walkthrough – Tag overview, recipe management and alarm diagnostics.
- Safety Certifications – Documentation for OSHA, NFPA and insurance audits.
- Video Recordings – Optional screen captures and live demos for new‑hire onboarding.
Ready for a Smooth, On‑Time Start‑Up?
GAT Offers Custom Turnkey Finishing Systems
You may wonder, “How can a custom system be turnkey? Shouldn’t it be more complicated than a few steps of installation?” This may be a surprise, but this isn’t our first time creating and installing a new custom finishing system. Since 1958, our team invested countless hours developing seamless manufacturing, construction, and installation processes. We can install your entire system in only a handful of steps. Within a short period of time, your system can be ready to run your parts through and avoid any downtime past the original startup.
Benefits of Turnkey Finishing Systems
- Virtually no time is lost because of the installation efficiency.
- Our GAT team takes responsibility for most of the scheduling and labor involving your new system install.
- Relatively quick turnaround time with a new system being in place anywhere between one week to three months, depending on the size and scope of the system.
Modular Installation Accelerates the Timeline
Our GAT team uses a modular installation approach that helps us stay on time and on budget. A majority of all GAT installations are completed by our full in-house install crew. Approximately 90% of their work is specific to GAT and the team’s vast experience spans more than 30 years in the business. When your new system is ready for installation, it’s loaded at GAT using industry-standard rigging and transported to your manufacturing site. Our installation covers all the final details and gets your system fine-tuned for optimal efficiency.
Frequently Asked Questions
Do I need to provide riggers?
GAT can supply a full‑service install crew or work alongside your preferred riggers.
Will production stop during install?
We stage work to minimize downtime; many lines install in segmented areas without full shutdown.
What if issues arise after start‑up?
Remote PLC access and a dedicated support line connect you to engineers within minutes.