When you’re looking at equipment for industrial pretreatment, like parts washers, you might think stainless steel is the only way to go. It’s tough, right? But actually, there’s a different material that’s been gaining a lot of traction, and for good reason: polypropylene. This plastic might seem like a strange choice at first glance, but for many applications, a Polypropylene Washer really does beat out its metal cousins. Let’s dig into why this plastic is often the better pick for these systems.
Key Takeaways
- Polypropylene offers great resistance to chemicals, which helps parts washers last longer.
- It’s a strong material that holds up well over time, even with constant use.
- Using polypropylene can save you money upfront and on upkeep.
- Polypropylene helps make the washing process more effective and cleaner.
- It’s a more environmentally friendly option compared to some other materials.
Understanding Polypropylene’s Inherent Advantages
Polypropylene washers are gaining traction as superior alternatives to stainless steel in pretreatment processes. This shift is largely due to polypropylene’s unique set of inherent advantages, which directly address common challenges in industrial washing applications. Let’s explore these benefits in detail.
Superior Chemical Resistance of Polypropylene Washer
One of the most compelling reasons to choose polypropylene is its exceptional resistance to a wide array of chemicals. Unlike stainless steel, which can corrode when exposed to certain acids, chlorides, or other aggressive substances, polypropylene remains largely unaffected. This makes it ideal for pretreatment processes involving harsh cleaning agents or degreasers.
- Resistant to acids
- Resistant to bases
- Resistant to solvents
Polypropylene’s inert nature minimizes the risk of chemical reactions that could compromise the integrity of the washer or contaminate the parts being cleaned. This is especially important in industries where maintaining purity and preventing cross-contamination are critical.
Exceptional Durability and Longevity
Beyond chemical resistance, polypropylene boasts impressive durability. It’s a tough material that can withstand the rigors of continuous use in an industrial setting. Polypropylene exhibits remarkable fatigue resistance, allowing it to endure repetitive flexing and bending without cracking or breaking. This translates to a longer lifespan for the washer and reduced downtime for repairs or replacements.
Cost-Effectiveness in Manufacturing
Polypropylene offers significant cost advantages compared to stainless steel. The material itself is generally less expensive, and the manufacturing processes involved in creating polypropylene washers are often simpler and more efficient. This leads to lower overall production costs, making polypropylene washers a more budget-friendly option without sacrificing performance. The lower density of polypropylene also contributes to reduced shipping costs.
Material | Relative Cost | Manufacturing Complexity | Weight |
---|---|---|---|
Stainless Steel | Higher | More Complex | Higher |
Polypropylene | Lower | Simpler | Lower |
Optimizing Pretreatment Processes with Polypropylene
Polypropylene washers are changing how we think about pretreatment. They’re not just a cheaper alternative; they can actually make the whole process better. Let’s look at how.
Superior Chemical Resistance of Polypropylene Washer
Polypropylene’s resistance to a wide range of chemicals is a game-changer. This means fewer compatibility issues and a longer lifespan for your equipment. Traditional metal washers can corrode, leading to contamination and costly downtime. Polypropylene? It just keeps going. For example, in processes involving acids or bases, polypropylene shows minimal degradation compared to stainless steel, which can pit and corrode over time. This inherent resistance reduces the need for frequent replacements and minimizes the risk of process contamination. This is especially important when dealing with industrial recyclers who need to optimize process settings.
Exceptional Durability and Longevity
Don’t let the fact that it’s plastic fool you; polypropylene is tough. It can handle a lot of wear and tear, making it a reliable choice for pretreatment systems. It resists cracking, impact, and abrasion, which are common problems in harsh industrial environments. Plus, it doesn’t rust, so you don’t have to worry about that. The durability of polypropylene translates to fewer repairs and replacements, saving you money in the long run.
Cost-Effectiveness in Manufacturing
Polypropylene is easier and cheaper to work with than stainless steel. This means lower manufacturing costs for washers and other components. These savings can then be passed on to the customer, making polypropylene systems a more budget-friendly option. The lower cost doesn’t mean lower quality; it just means a smarter use of materials and manufacturing processes.
Switching to polypropylene can significantly reduce your upfront investment. The material itself is less expensive, and the manufacturing processes are simpler. This allows for faster production times and lower labor costs, all of which contribute to a more affordable system.
Enhanced Adhesion and Surface Preparation
Polypropylene’s surface properties can actually help with adhesion in subsequent coating or painting processes. It can be easily treated to create a surface that promotes better bonding, leading to a more durable and long-lasting finish. This is a big advantage over stainless steel, which often requires more extensive surface preparation. Here’s a quick comparison:
Material | Surface Preparation Required | Adhesion Performance |
---|---|---|
Stainless Steel | Extensive (e.g., etching) | Moderate |
Polypropylene | Minimal (e.g., corona) | High |
Reduced Contamination Risks
Because polypropylene is so resistant to chemicals, it’s less likely to leach contaminants into the pretreatment solution. This is especially important in industries where purity is critical, such as electronics manufacturing or pharmaceuticals. A cleaner process means a better end product and fewer quality control issues. Polypropylene’s inert nature minimizes the risk of introducing unwanted substances into the system, ensuring a more consistent and reliable pretreatment process.
Improved Process Efficiency
Polypropylene’s properties can also lead to improved process efficiency. Its smooth surface reduces friction, which can lower energy consumption. It’s also lightweight, making it easier to handle and install. All of these factors contribute to a more streamlined and efficient pretreatment operation. Here are some ways polypropylene can improve efficiency:
- Reduced energy consumption due to lower friction.
- Faster installation and maintenance due to its lightweight nature.
- Less downtime due to its resistance to corrosion and wear.
- Simplified cleaning procedures due to its smooth, non-stick surface.
Addressing Challenges in Material Selection
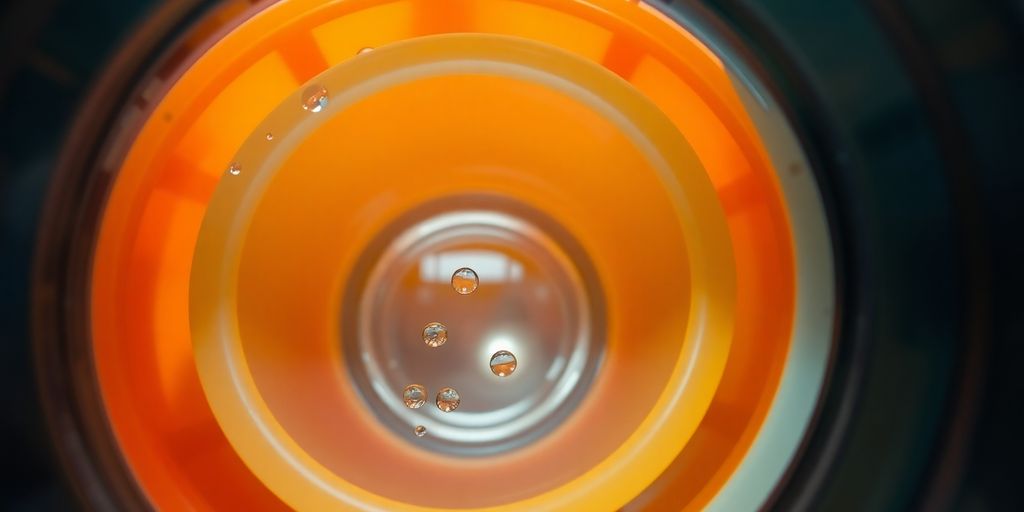
Choosing the right material for a washer system is more complex than it looks. It’s not just about picking something cheap; you have to think about how it will hold up over time, what chemicals it will be exposed to, and even how it will affect the final product. Let’s break down some of the key challenges.
Mitigating Corrosion and Degradation
One of the biggest advantages of polypropylene is its resistance to corrosion, but that doesn’t mean it’s immune to everything. Certain chemicals and prolonged exposure to UV light can still cause degradation. It’s important to select a polypropylene formulation that is specifically designed for the chemicals and environment it will be exposed to. For example, if your washer system is used with strong acids, you’ll need a polypropylene that’s formulated to withstand those conditions. Regular inspections can also help catch early signs of degradation before they become major problems.
Ensuring Material Compatibility
It’s not enough for the washer material to be resistant to the chemicals; you also have to make sure it won’t react with the parts being cleaned. Some plastics can leach chemicals that contaminate the parts, or they can cause discoloration. Compatibility testing is a must. Here’s a simple table to illustrate:
Material | Compatible With | Incompatible With |
---|---|---|
Polypropylene | Many acids, bases | Strong oxidizers |
Stainless Steel | Most chemicals | Halides |
Other Plastics | Varies | Varies |
Considerations for High-Temperature Applications
Polypropylene has a lower temperature resistance than metals like stainless steel. While GAT offers energy-efficient polypropylene washers, it’s crucial to stay within the material’s operating temperature range. Going above that range can cause the plastic to soften, warp, or even fail completely. If you need a washer system that can handle high temperatures, you might need to consider alternative materials or look into advanced polypropylene formulations that are designed for higher heat resistance.
Choosing the right material is a balancing act. You have to weigh the cost, the chemical resistance, the temperature resistance, and the compatibility with the parts being cleaned. It’s not always easy, but doing your homework upfront can save you a lot of headaches down the road.
The Economic Benefits of Polypropylene Washer Systems
Polypropylene washer systems are gaining traction, and for good reason. It’s not just about the material itself; it’s about the bottom line. Companies are always looking for ways to cut costs without sacrificing quality, and polypropylene offers a compelling case.
Lower Initial Investment Costs
One of the most immediate benefits is the lower upfront cost. Polypropylene is generally cheaper to produce than stainless steel. This translates directly into savings when purchasing a new washer system. The difference can be significant, especially for larger operations or those needing multiple units. This allows businesses to allocate resources to other areas, like advanced polypropylene research and development.
Reduced Maintenance and Repair Expenses
Polypropylene’s resistance to chemicals plays a big role here. Because it doesn’t corrode like steel, you’ll spend less time and money on repairs and replacements. Think about it: no rust, no pitting, and fewer breakdowns. This leads to less downtime and more consistent operation.
Consider these points:
- Fewer replacement parts needed.
- Reduced labor costs for repairs.
- Less frequent maintenance schedules.
Energy Efficiency in Operation
Polypropylene has a lower thermal conductivity than stainless steel. This means it doesn’t transfer heat as readily. In washer systems, this can translate to energy savings. The system requires less energy to maintain the desired temperature, leading to lower utility bills over time.
Switching to polypropylene can have a noticeable impact on your energy consumption. While the exact savings will vary depending on the specific application and system design, the potential for reduced energy costs is a significant advantage.
Environmental Impact and Sustainability
It’s not just about cost savings or better performance; thinking about the environment is a big deal too. Polypropylene washers have some real advantages when it comes to being eco-friendly. Let’s take a look.
Recyclability of Polypropylene Washer Components
One of the best things about polypropylene is that it’s recyclable. Unlike some other plastics that end up in landfills, polypropylene can be reprocessed and used to make new products. This reduces the demand for new raw materials and helps to conserve resources. It’s a win-win. Recycling polypropylene helps close the loop and promotes a circular economy.
Reduced Waste Generation
Polypropylene washers are often more durable than their metal counterparts, meaning they last longer. This extended lifespan directly translates to less frequent replacements and, consequently, less waste. Plus, because polypropylene is lighter than stainless steel, there’s less material used in the first place. This all adds up to a smaller environmental footprint. industrial finishing equipment can help reduce waste generation.
Compliance with Environmental Regulations
Companies are under increasing pressure to meet environmental regulations, and using polypropylene washers can help. Polypropylene is free from many of the harmful chemicals found in other materials, making it easier to comply with regulations related to hazardous waste and emissions. Plus, the recyclability of polypropylene can contribute to achieving sustainability goals and improving a company’s environmental performance.
Choosing polypropylene can be a step towards a greener operation. It aligns with the growing emphasis on sustainability and responsible manufacturing practices. By opting for materials with lower environmental impacts, companies can demonstrate their commitment to protecting the planet and meeting the expectations of environmentally conscious customers.
Advanced Polypropylene Formulations for Washers
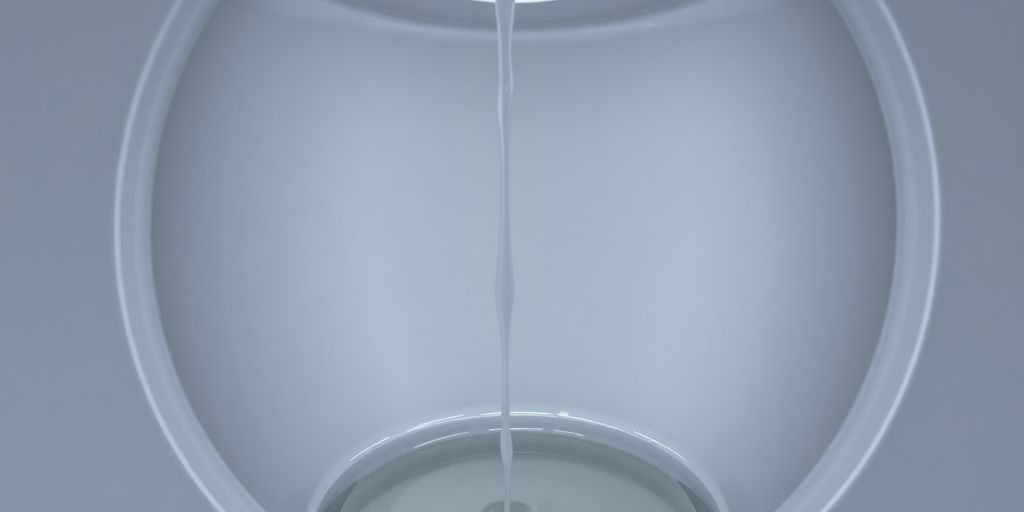
Polypropylene’s versatility really shines when you start tweaking its formula. It’s not just about using plain PP anymore; we’re talking about some serious upgrades to make it even better for demanding applications like finishing system components in washers. These advanced formulations aim to boost specific properties, like strength, chemical resistance, and temperature stability, opening up new possibilities for PP washers.
Reinforced Polypropylene Composites
Think of reinforced PP as PP on steroids. By adding materials like glass fibers, carbon fibers, or even mineral fillers, you can dramatically improve its mechanical properties. This means a stiffer, stronger washer that can handle more stress and last longer. For example, adding wollastonite can significantly increase tensile strength. These composites are especially useful in applications where the washer needs to withstand high pressures or abrasive chemicals. The type and amount of reinforcement can be tailored to meet specific performance requirements.
Surface Treatment Technologies
Sometimes, the base material is good, but the surface needs a little help. That’s where surface treatments come in. These treatments can modify the surface properties of the PP to improve adhesion, wear resistance, or even chemical inertness.
- Chemical etching can create a rougher surface for better paint or coating adhesion.
- Plasma treatment can alter the surface energy, making it more receptive to bonding.
- Applying a protective coating can shield the PP from harsh chemicals or UV radiation.
Surface treatments are a cost-effective way to enhance the performance of PP washers without changing the bulk material properties. They allow you to fine-tune the surface to meet the demands of a specific application.
Innovations in Polymer Blending
Polymer blending is like mixing different types of plastic to get the best of both worlds. By blending PP with other polymers, you can create materials with unique combinations of properties. For instance, blending PP with a more flexible polymer can improve its impact resistance, while blending it with a more heat-resistant polymer can increase its service temperature. Polymer blending allows for a high degree of customization, enabling the creation of PP formulations tailored to very specific washer applications. It’s all about finding the right mix to achieve the desired balance of properties.
Case Studies: Successful Polypropylene Washer Implementations
Automotive Industry Applications
Polypropylene washers are making waves in the automotive sector. Think about it: cars need to be durable, but also lightweight to improve fuel efficiency. Polypropylene hits that sweet spot. One major car manufacturer switched to polypropylene washers in their pretreatment line for body panels and saw a significant drop in corrosion-related warranty claims. They also reported a smoother paint finish, likely due to the enhanced surface preparation achieved with the plastic washers. It’s not just about saving money; it’s about building better cars. The move to polypropylene also cut down on downtime because the washers are less prone to jamming and wear compared to their metal counterparts. This has led to increased throughput and reduced operational costs. It’s a win-win.
Electronics Manufacturing Solutions
Electronics manufacturing is all about precision and cleanliness. Even the tiniest bit of contamination can ruin a whole batch of circuit boards. That’s where polypropylene washers shine. They’re naturally resistant to many of the harsh chemicals used in electronics cleaning processes. A large electronics company implemented polypropylene washers in their industrial part cleaning systems for cleaning printed circuit boards (PCBs) before assembly. The results? A noticeable decrease in defects related to surface contamination. Plus, the gentler action of the plastic washers reduced the risk of damaging delicate components. Here’s a quick rundown of the benefits they saw:
- Reduced contamination-related defects by 15%
- Lowered chemical consumption by 10% due to better rinsing
- Extended washer lifespan by 20% compared to stainless steel
General Industrial Pretreatment
Polypropylene washers aren’t just for fancy industries like automotive and electronics. They’re also finding a home in general industrial pretreatment applications. From cleaning metal parts before powder coating to preparing surfaces for adhesive bonding, polypropylene is proving its worth. The versatility of polypropylene means it can handle a wide range of cleaning solutions and temperatures. One company that manufactures metal furniture switched to polypropylene washers and saw a big improvement in the quality of their powder coating. They were struggling with rust spots appearing under the coating, but the switch to plastic washers eliminated that problem. It’s a simple change that made a big difference. The company also noted that the polypropylene washers were much easier to handle and replace, which saved time and effort for their maintenance team.
Switching to polypropylene washers was one of the best decisions we made. It improved our product quality, reduced our costs, and made our lives easier. I wish we had done it sooner.
Want to see how our polypropylene washers have helped other businesses? Check out our success stories! You’ll find real-world examples of how these washers make a big difference. Ready to improve your own operations? Request a quote today and let’s get started!
The Clear Choice for Pretreatment
So, when you look at everything, it’s pretty clear that polypropylene washers are a smart move for pretreatment. They just handle those tough chemicals better than stainless steel, and they don’t cost as much to get going or keep running. Plus, they’re lighter, which makes them easier to work with. It’s not just about saving money, though. These plastic washers also help make the whole process smoother and more reliable. For anyone serious about getting their parts ready for the next step, going with polypropylene just makes sense. It’s a simple choice that really pays off in the long run.
Frequently Asked Questions
Why is polypropylene better than stainless steel for these washers?
Polypropylene is a type of plastic that’s really good at handling different chemicals without breaking down. This makes it perfect for washer systems that use strong cleaning liquids. It also lasts a long time and costs less to make than metal parts.
How does using polypropylene help with cleaning and preparing surfaces?
Using polypropylene helps things stick better to surfaces because it allows for a cleaner wash. It also means fewer bad things get into the cleaning process, and the whole washing operation runs more smoothly and quickly.
What are some challenges when choosing materials for these systems?
Sometimes, picking the right material can be tricky. We need to make sure the plastic doesn’t get ruined by the chemicals or heat. We also have to think about how hot the washing process gets to make sure the polypropylene can handle it.
Are there any money-saving benefits to using polypropylene washers?
Polypropylene systems usually cost less to buy at first. They also don’t need as much fixing or upkeep, which saves money over time. Plus, they can even help save energy during operation.
Is polypropylene good for the environment?
Yes! Polypropylene parts can often be recycled, which means less trash. Using them also helps companies follow environmental rules and be more eco-friendly.
Are there different kinds of polypropylene used for washers?
Scientists are always making polypropylene even better. They’re creating stronger versions by mixing it with other materials, and they’re finding new ways to treat its surface to make it perform even better in tough conditions.